Lean and Kaizen are some of the common techniques used to optimize processes. However, document libraries that contain useful information are neglected. Many times, best practices, lessons learned, maintenance records, and work instructions are stored in the virtual bookshelf or tucked away in ‘shared’ directory. Empower your teams to capture valuable knowledge from standards, best practices, lessons learned, checklists, and experienced employees. Instead of searching for information, important knowledge is effortlessly and continuously being captured, validated, and reused, which positively influences technical decision-making, saving the organization valuable resources and time.
Operations
Auros IQ Solutions
Audits of plant health criteria within and across plants
- Built-in validation, data acquisition, tracking, auditing, and evidence-gathering capabilities suitable for plant floor systems evaluations
- Process visualization allows teams to visualize when and how to conduct both synchronous and asynchronous readiness review events
- Look-Across one click to access a detailed report of all past implementations of the readiness criteria including status, evidence, discussion, issues, and attachments
- Dynamic Open Issue Reporting and Tracking
- Robust automated evidence gathering for effortless and worry-free auditing
- Off-line capable
- XLS integration
Comprehensive collaborative project management toolset
- Team’s Project activities in one spot
- Team KPIs and customer reports, analytics, and shared dashboard
- Both Standard Work and Ad Hoc Work synchronized with Lean/Kan Ban methodology
- Interactive and visual standard process tracking and reporting
- Generative Gantt Chart derived from deliverables and logical process plans
- Automated system and notifications ensure individuals and teams receive deadline reminders, updated task information
Efficiently and effectively deploy lessons across locations or suppliers to implement improvements or prevent the recurrence of failures
- Robust re-use and automated provision of Lessons to your projects when and where needed.
- Continuous Knowledge Capture
- Customizable templates and workflows
- Stream-lined Authorship, Review, and Approval
- Automated Knowledge Health Insights
Operations audits of production criteria across systems
- Automated delivery and tracking of operational standards to audit processes
- Built-in validation, tracking, auditing, and evidence-gathering capabilities
- Process visualization allows teams to visualize when and how to conduct both synchronous and asynchronous readiness review events
- Look-Across- one click to access a detailed report of all past implementations of the operational criteria including status, evidence, discussion, issues, and attachments
- Dynamic Open Issue Reporting and Tracking
- Robust automated evidence gathering for effortless and worry-free auditing
- Off-line capable
- XLS integration
Automated dynamic provisioning of interactive work instructions to plant personnel as they are needed.
Stream-lined Authorship, Review, and Approval
REST base services to integrate into plant floor systems
Built-in validation, tracking, auditing, and evidence-gathering capabilities
Comprehensive and highly configurable ticketing, issue, and case management
- Issue aging and other analytics
- AI tools for clustering and risk identification
- XLS integration
- Widely used at the OEM level
Effective Systems Integration
Connect Auros IQ to your web-based API system including PLM workflows, CAD / CAE, and others
Unique Approach, Transformative Results
Developed by Auros Knowledge Systems, Knowledge Aware is a comprehensive approach to continuously collect, deliver, and actively apply trusted knowledge directly into an employee’s workflow. Unlike traditional knowledge management strategies, this unique approach not only captures knowledge from best practices, employee knowledge, lessons learned, methods, requirements, standards, and techniques—but also delivers the knowledge when and where it’s needed. Auros IQ operates on the basis of the Knowledge Aware approach to improve technical decision-making and analysis, and increase organizational efficiency and product quality.
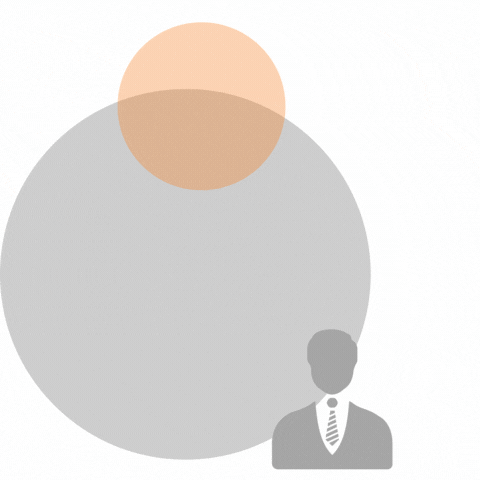
Schedule A Free Briefing
Your assigned consultant will brief you on Auros IQ and the unique Knowledge Aware approach, which powers up critical engineering processes. You will learn how it works, how other organizations use it, and how it can transform your organization’s processes.